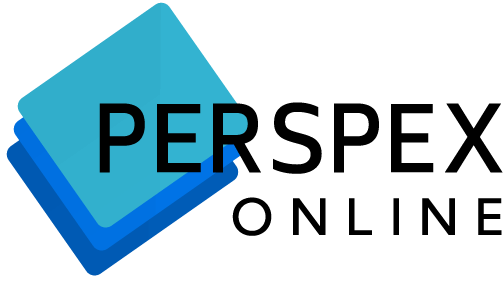
We don’t just sell perspex online, we can design and manufacture virtually any plastic item or component regardless of the industry. Our team of experts in plastic fabrication can also help you with the best choice Materials for your project.
We’ve listed our most frequently asked questions below. For any other enquiries call us during our business hours Monday to Friday 7:30 am to 4:00 pm.
Nearly all boat screens are made from PERSPEX (Acrylic) due to its UV resistance and durability. This material is easy to maintain with small scratches taken out with “Brasso”. LEXAN (Polycarbonate) on the other hand has a lot higher impact strength than acrylic, it has a coating on each side to give it UV resistance and can come with an Abrasion resistant surface…. this a lot more expensive product to use for this purpose.
Both Corflute & PVC Foam is a light weight, cheap material for model building.
HDPE in a natural colour (Milky colour) is excellent for use as a chopping board for gutting fish or slicing up a steak for lunch.
We recommend Boatboard (Seaboard) which is a WHITE UV resistant HDPE material designed for boat applications.
Talk to us and we will recommend what you should use for the application. We supply and cut 3, 4.5, 6, 8, & 10mm thick CLEAR Perspex cut to size, to your requirements in any thickness.
There are few differences between the physical properties of Cast Perspex Acrylic and Extruded Perspex Acrylic sheets. Both show excellent resistance to natural ageing. The main differences lie in their thermal and chemical properties and the way they are processed and used. The two materials are different in nature and respond differently to certain processes. The Cast manufacturing process leads to slight variations in the thickness of sheets whereas the thickness of Extruded sheet varies very little, if at all. Cast has an isotropic response to temperature with a maximum shrinkage of 2% in all directions. However, the extrusion process applied to Extruded sheet leads to differences in shrinkage depending on the thickness and direction of extrusion. Extruded acrylic sheet has reduced mechanical properties, however it does give process advantages when heating, bending and vacuum forming, and has a better thickness tolerance than cast acrylic sheet Extruded sheets are ideal for general glazing applications and the much lower viscosity when hot, makes it more ductile than Cast Acrylic. Cast Acrylic sheets offer greater thermal stability and better resistance to crazing when exposed to solvents. The thermoforming range for cast sheets is wider. They can be reworked hot, which is not always possible with extruded sheets. The surface finish, flatness and optical properties of Cast Acrylic are all superior to those of Extruded Acrylic sheets.
The surface should not generally require cleaning until after fabrication. For general purpose cleaning, the sheet should be washed simply with clean cold water to which a little detergent has been added. The use of any solvents such as methylated spirits, turpentine, white spirit or proprietary window cleaning products is neither necessary nor recommended. Before screen printing it is advisable to wash the sheet surfaces to be printed on with clean fresh water using a chamois leather or soft cloth. This has the advantage of removing all traces of static charge from the sheet after removal of the film which might otherwise attract dust.
It will soften if heated above 80 C. Considerable heat can be generated by machining, causing stress, so it is therefore very important that heat build-up is kept to a minimum.
Various coolants can be used including water and water/air mists, soluble oils and compressed air. Soluble oils must be oil-in-water emulsions and must not contain solvents which may cause stress cracking.
To achieve a good finish all cutting tools must be kept sharp. Most hand tools designed for use with wood or soft metals are suitable for use with acrylic except laminate cutters, guillotines and blanking dies. Most power tools can be used and HSS tools bits are suitable to achieve a good cut finish. For lengthy runs, tungsten carbide tipped blades and tool bits are recommended for long life.
For small jobs fine-toothed hand saws such as fret saws or hack saws are recommended. The work must be securely fixed and only light pressure applied. Powered saws with blades having alternative teeth beveled, as for aluminium, are particularly recommended for sawing acrylic as are band saws, jig saws and fret saws. For further recommended conditions for sawing acrylic, please download the Perspex Acrylic Sheet Workshop Handbook.
Yes, they may be laser cut to achieve very complex and intricate shapes.
Standard woodworking twist drills can be used for all normal drilling work with perspex acrylic. Whenever possible, the work should.
Standard taps and dies may be used for cutting screw threads in acrylic but whenever possible, coarse threads are preferred as they are less liable to damage. Threads must not be overstressed and it is not advisable to thread acrylic if frequent dismantling is likely. In such conditions, threaded metal inserts are recommended.
We can offer Power Buffing, Diamond Polishing and Flame Polishing services. Diamond Polishing can be used for straight edges and gives excellent results without the rounded edges often produced by buffing. Flame Polishing is ideal for polishing thin edges of acrylic, especially clear extruded sheet for point-of-sale items because its fast and effective. For a ultimate high gloss finish and for bespoke acrylic shapes we can also hand polish the acrylic parts.
For minor scratches you can purchase Novus 2 or Novus 3 scratch remover polish from us which can restore the finish. Please click on the link for further information on Novus Polishes.
Our Perspex acrylic sheets do not go yellow in the sun and Perspex offer a 10 year guarantee on discoloration. Perspex is an international brand which stands for quality, innovation and design. Perspex has an unrivalled reputation for product performance and are regarded as the leading acrylic sheet material in the world.
Acrylic sheets achieves a UK Class 3 fire rating.
Tensol 12 is a single component cement which hardens due to solvent evaporation to produce a dear bond in cast acrylic sheets Tensol 12 is only recommended for internal signage and low strength bonds. Tensol 70 is a two part catalyst cement which cures =: ambient temperatures to produce high strength bonds to acrylic sheet and offers excellent weathering resistance. You can [Mtitaaa both tensol adhesives from us.
You can purchase custom size acrylic sheets 24/7 from www.plasticsonline.net.au online ordering web site.Alternatively you can call via telephone during office hours 7.30AM to 4.00PM weekdays. Molendinar Qld. Ph. 07 5564 6744 OR Burleigh Heads Qld. 07 5535 7544.
Yes, our fabrication department can provide bespoke cutout shapes to your specification. You can e-mail us drawings in various computer drawing formats (jpg, ai, dwg, dxf, etc. See fabrication pages for more detail) or even provide hand sketch drawings and :..' in-house design team will do the rest.